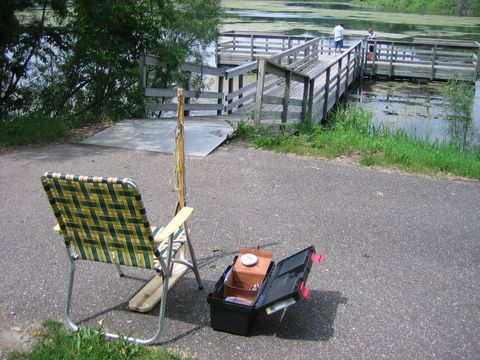
First, of course, my disclaimer: I am not a perfectionist and I am not a woodworker. My only aim in building this contraption was functionality, I was not about to invest a lot of effort in a prototype that might not even work.
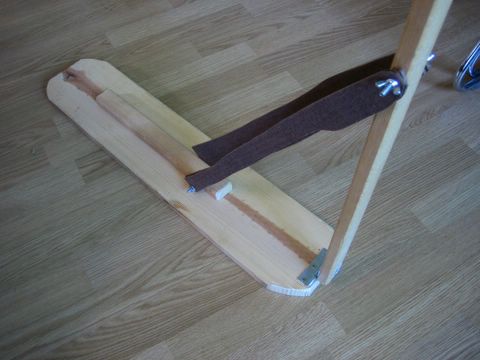
The upright is hinged on the floorboard so that the whole thing can collapse when the two diagonals are disengaged at the top.
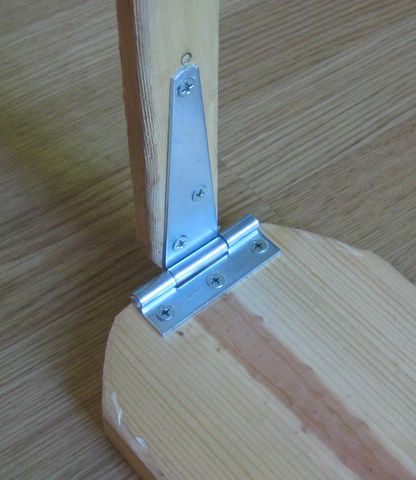
The two diagonals are fixed to the floorboards with 'studs' that screw into the wood and then have a protruding bolt. The diagonals can move freely on these bolts so that they can fold down and lie flat on the floorboard - to enable this, their bottom ends are rounded so as not to get stuck against the floorboard.
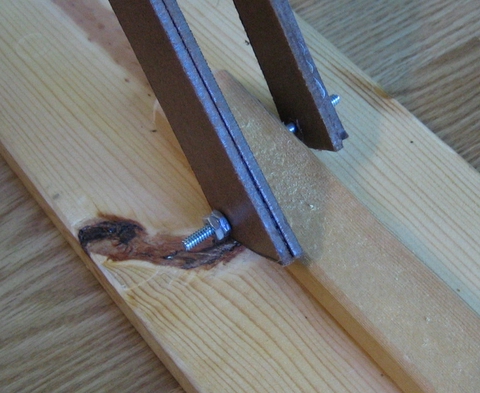
At the top the diagonals are fixed to the upright with the same studs, but this time with wingnuts so that they can easily be detached. At both the bottom and top, they are purposefully not in line so that the studs do not screw into each other in the middle of the upright.
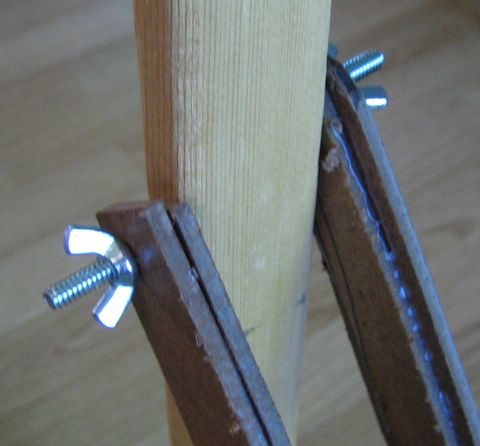
I might still make some modifications to the top of the upright - the 'working end'. The two hooks work fine to hook the braiding on, but to take up the already braided excess, I need a better plan... so look out for an update in a month or two...!
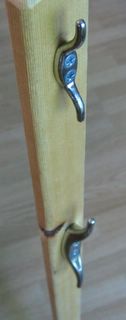
Happy braiding!